5 Ways to Further Automate the Manufacturing Industry
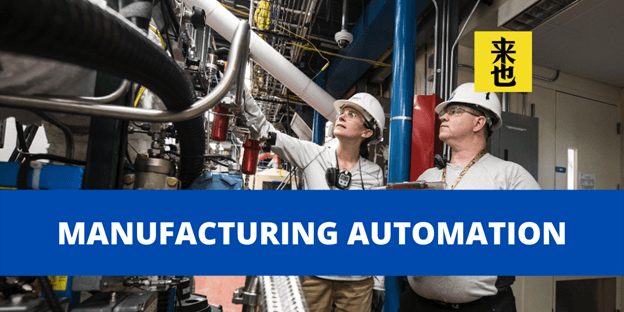
The manufacturing industry is no stranger to automation. Automation has greatly benefited the assembly line, allowing manufacturers to boost efficiency, accuracy, and productivity when building physical products. However, a report made by Research and Markets estimates that the industry will decrease from $846.1 billion in 2019 to $818.6 billion in 2020 due to COVID-19. As manufacturers are faced with a slowing economy, cutting costs and improving efficiency and accuracy are crucial in keeping a competitive edge.
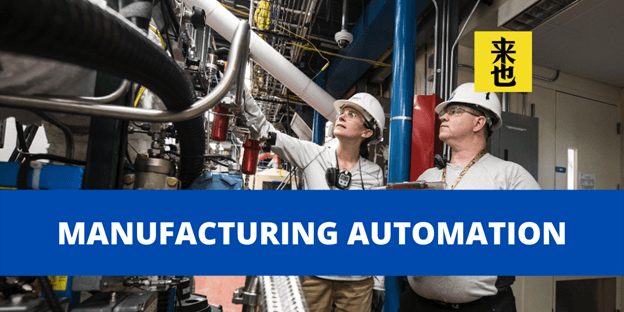
To further improve business, manufacturers are turning to other forms of automation, specifically RPA (robotic process automation), software that can emulate human operations on a PC according to predefined rules. Extending automation beyond the physical assembly lines, manufacturers can benefit from computer robots that can handle repetitive, manual tasks that govern the manufacturing process. We offer manufacturers a reliable, secure RPA product Laiye UiBot. Equipped with AI technology such as OCR (optical character recognition), Laiye UiBot is a strong assistant that can work 24/7, all year round effortlessly with near-perfect efficiency and accuracy. In this article, we explore 5 different scenarios where manufacturers can automate with Laiye UiBot.
Scenario 1: BOM (bill of materials) management
Every manufacturer has to have a BOM that lists the components needed to manufacture a product. Various versions of the BOM exist, such as engineering, manufacturing, and purchasing BOMs. Updating the BOM manually requires several steps:
1, Log into the company's ERP(enterprise resource planning) system
2, Access the BOM spreadsheet
3, Make changes to one version of the BOM, which may require recalculation of quantity or a change in other items
4, Propagate the changes to other versions of the BOM
5, Check for consistency across all BOMs
Updating or creating a new BOM manually is tedious and time-consuming. However, the biggest risk arises from human error. Since the BOM is a central reference for all departments, discrepancies in the BOMs or general mistakes can cascade and create disastrous consequences such as missing parts, incorrect purchases, and huge losses. With Laiye UiBot, these mistakes can be avoided. With login credentials, Laiye UiBot can automatically access the BOM and uniformly change and recalculate all versions of the BOM to ensure consistency. It can also keep a log of revisions for future review and compare the BOMs to check for disagreements, all with very high efficiency and accuracy.
Scenario 2: Data migration
Whether the company is simply moving from an old system or has recently acquired another business, manufacturers often need to move, and sometimes transform, data from legacy systems to new systems using ETL (extract, transform, load).
1, Log into the old system
2, Process and extract the source information
3, Transform the information by mapping its format to the target system
4, Introduce the data to the new system
5, Check that the migration is successful and complete
Migrating data is a complicated process when done manually and can lead to errors that can pile up. Not only is the process a time and financial commitment, but it is also often highly inaccurate, meaning the transfer could be incomplete or incorrect. Laiye UiBot significantly reduces risks by streamlining the process. Capable of reading both structured and unstructured data with a wide variety of file formats, Laiye UiBot's recognition capabilities allow it to extract relevant information, convert it, and effortlessly input it into the new system.
Scenario 3: CRM (customer relationship management) and order processing
Having an effective CRM is essential to a business—and manufacturing is no exception. When a manufacturer has a potential customer, the sales team needs to manage information for the customer:
1, Estimate a price
2, Search for product availability
3, Process an order
4, Generate quotations
5, Determine shipping times
This process is tedious and a waste of the sales team's effort and time when they could be servicing the next client. Laiye UiBot can handle the manual work by automatically checking prices, availability, and shipping times and cross-checking with other software to confirm this information; extracting information from orders, whether paper-based or digital; and inputting the information into the CRM system.
Scenario 4: Regulatory compliance
Manufacturers must adhere to regulations to avoid legal and reputational repercussions. However, this entails several difficult tasks:
1, Track all activity happening in the company, including who, what, when, where, and how something was completed
2, Ensure that tasks are carried out uniformly according to the legal standard
3, Prepare for compliance audits
4, Change processes accordingly whenever regulations change
Human error is inevitable, meaning that some tasks may not be carried out at the legal standard due to fluctuations in human performance. Keeping track of all activity is a difficult, monotonous task that is hard to guarantee. Moreover, adapting to new regulations takes time. Laiye UiBot can help manufacturers meet regulations by keeping a real-time log of all activities that occur, including who performed the activity and when. Doing so prepares the company for auditing and provides a clear record. Moreover, since Laiye UiBot operates according to rules, it can perform the same task in a standard way and can be changed immediately once regulations change.
Scenario 5: Production inventory
To ensure steady production, manufacturers need to be aware of their production inventory. Making sure there is no shortage or surplus is a difficult task:
1, Check current inventory levels for different components
2, Log into the ERP system
3, Update the inventory levels in the system
4, Purchase more materials when inventory levels are low
The difficulty in manually managing inventory is that management cannot happen in real-time. This introduces time lags which may delay production. Moreover, it is difficult to determine how much to purchase. Laiye UiBot can monitor inventory levels in real-time and alert staff members when inventory falls below a certain threshold in the system. Staff members could then promptly purchase more materials or have the robots automate the purchasing process. Additionally, robots can synthesize data over purchasing cycles to determine supply and demand, and thus optimize the level of purchase.
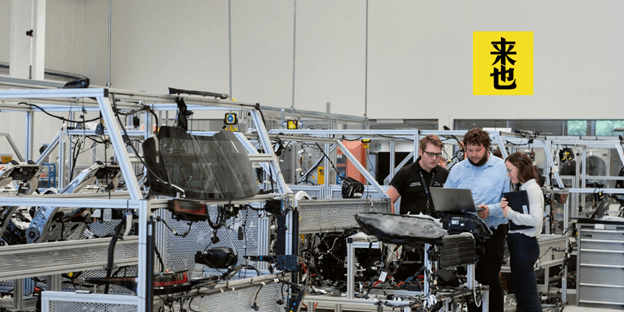
Start automating today
Due to how flexible RPA is, Laiye UiBot can be tailored to help automate many more tasks than just those listed above. By improving accuracy and efficiency, Laiye UiBot helps liberate human labor from tedious, low-value work and allows them to pursue more productive work. These changes translate into greater savings and higher revenue for manufacturers. In just a few hours with the help of our professional team, you can start building your own robots beyond the assembly line.
About Laiye
Laiye, founded in 2015 by Ivy League Ph.D. graduates, is committed to being a leading Smart Robot platform with global influence in the era of human-robot collaboration.
Our portfolio of high-quality, secure products and services covers RPA Solution, including Laiye UiBot (an RPA product), Laiye Wulai (an enterprise chatbot platform), and Xiaolai (a companion robot). Join us on LinkedIn, follow us on Facebook, or visit laiye.com/en.